

How to Polish Concrete Flooring
Polished concrete flooring is a popular choice among property owners for new construction and renovations alike. Its natural strength and resilience make it easy to clean and maintain, while its versatility offers lots of choices in terms of style and aesthetics.
The polishing process requires the proper equipment, tooling, chemistry, and training to achieve the desired results. The experts at Jon-Don have prepared this helpful guide to give you an overview of the concrete polishing process and necessary equipment.
In this guide, we’ll share:
- Some of the top advantages of concrete flooring
- What you’ll need to polish a concrete floor
- The basic steps for concrete polishing
For assistance with your concrete polishing project, please contact a member of our team at 800-556-6366.
The Advantages of a Polished Concrete Floor
Polished concrete floors offer a variety of benefits and advantages over other types of flooring for both residential and commercial uses.
Durability
Polished concrete is an exceptionally durable and attractive flooring choice for both homes and businesses. A properly executed polished concrete flooring system includes a concrete densifier that reacts with the calcium hydroxide in the concrete. This creates a stronger wearing surface from the original pour, preventing dusting and deterioration. There are a variety of penetrating and/or film-forming guards and sealers that can be incorporated into the system depending on the end user's expectations, which can help reduce staining and chemical damage.
Affordability
Polished concrete flooring can be a more cost-effective solution when compared to other types of floor coverings, such as carpet, tile, or wood. The life cycle is typically longer and maintenance costs are also historically lower.
Versatility
Polished concrete flooring is an extremely versatile choice and allows the property owner to choose the level of sheen, from satin to high gloss; and aggregate exposure, from large decorative stone to cream finishes. Additionally, dyes and intricate patterns can be added to concrete flooring to create a unique look.
Easy to Clean
A properly polished concrete floor is easier to clean than many other types of flooring. By closing the pores and sealing the joints, there are few areas where dirt and grime can cling.
Keep in mind that "low maintenance" does not mean "no maintenance." Implementing proper post-installation programs will help to extend the life cycle of polished concrete flooring and limit the need to refresh the finished product.
Consult your local Jon-Don concrete rep for guidance on maintenance products and procedures to ensure your floor stays looking new for years to come.
What You’ll Need to Polish a Concrete Floor
Concrete Floor Grinder
The best type of concrete floor grinder will depend on the job, location, power limitations, the desired outcome, and the concrete itself. For more in-depth information on selecting the right floor grinder, see our dedicated guide.
OSHA Approved Dust Collector
For jobs where you’re performing dry concrete grinding, polishing, cutting, or drilling, you must use an OSHA-compliant dust collector. Shop vacs, which were once a popular tool for collecting dust during concrete surface prep jobs, should not be used.
There are four critical dust collector rules you need to follow to avoid hefty fines. Dust collectors must:
- Be the right size. For hand grinding or tuck pointing applications, your dust collector must provide 25 CFM for every inch of cutting blade. For large walk-behind grinders, follow the recommendations specified by the manufacturer.
- Provide proper filtration. The air filter must provide 99% or greater filter efficiency. A HEPA vacuum is required for cleaning in between passes or general housekeeping.
- Have an internal filter-cleaning mechanism. The mechanism must be able to dislodge clogs and knock off accumulated dust without exposing workers.
- Have hoses that are in good working condition. Make sure the hoses have no kinks or tight bends that could restrict airflow.
Jon-Don offers a wide selection of OSHA-compliant dust collectors, as well as filtered, hoses, cords, and bags.
Diamond Tooling
Diamond tooling is comprised of manufactured diamonds embedded in a variety of metals, ceramics, and resins to hold the diamond matrix in place. Harder metal alloys are used for "hard bond" tooling and softer metal alloys are used for "soft bond" tooling.
Understanding Bond Strength
When working with a hard concrete floor, a softer bond diamond is used to keep the diamonds exposed and performing. Alternatively, a hard bond diamond is used on soft concrete floors to extend the life of the tool and prevent it from burning up too quickly. If a hard bond diamond is used on a hard concrete floor, the diamond will glaze over and stop performing.
To choose the right diamond tooling for your polishing project, it will be important to understand the concrete substrate you will be working with. A Mohs’ hardness test can help give you a good starting point as to the bond strength of your tools.
EXPERT TIP: Run your diamond for 10–15 minutes. Then, evaluate the amount of concrete dust produced, tipping your machine back to see how much of the diamond thickness has been reduced. If you have plenty of dust and little diamond use, you should be on the right track.
Understanding Tooling Grit Levels
Polishing concrete involves following a sequence of steps for proper refinement and requires more than one grit of diamond tooling. The process begins with a lower-grit diamond pad abrasive and progressively increases to finer grit levels with each pass.
This process is dependent on the specifications or expectations of the end user. Proper planning, realistic expectations, and mockups are crucial for a successful outcome. The experts at Jon-Don have provided a good starting point to build your system below, but it should be modified depending on the situation.
The polishing process is broken down into 3 steps;
- Grinding
Removing scratches and thin coatings, and preparing the surface.- 16/20 grit metal bond
- 30/40 grit metal bond
- 60/80 grit metal bond
- 120-150 grit metal bond
- Honing
Refining the floor and smoothing out the surface before polishing.- 50 grit transitional
- 100 grit transitional
- 200 grit transitional
- 400 grit transitional
- Polishing
Final polishing steps to enhance the floor’s reflectivity and gloss.- 800 grit resin
- 1500 grit resin
- 3000 grit resin
Ultimately, your specification and mock-ups will allow you to tailor your process to achieve the desired result.
Densifier
Concrete densifiers work by reacting with the calcium hydroxide in the concrete to form a calcium silicate hydrate, which fills the pores in the concrete and makes it denser. The active ingredient in most concrete densifiers is silicate or siliconate compounds. However, the delivery agent of this reactive compound changes depending on the situation, specification, timing, and skill level of the installation team.
Some basic formula variations of densifiers include:
- Sodium
- Potassium
- Lithium
- Colloidal
For help in choosing the right densifier for your floor, contact a Jon-Don concrete expert at 800-556-6366.
Basic Steps for How to Polish Concrete
The concrete polishing process involves using coarse diamond abrasives that grind the concrete to eliminate minor pits, blemishes, stains, and other imperfections as well as polish the floor to a high-gloss shine. Here’s how:
- Determine the surface’s hardness using a Mohs’ scale scratch test kit.
- Remove any existing coatings or adhesive residue using either the mechanical method (with a 16- or 20-grit diamond abrasive) or the chemical method as described in this article.
- Apply a resinous grout, crack, and joint filler as required. Metzger/McGuire is a leader in the concrete joint and crack repair industry and provides extensive literature on this topic. Consult your local Jon-Don concrete rep for hands-on training opportunities
- Use transitional tools to remove any scratches left behind by metal tooling.
- Polish the floor following the grinding/honing/polishing process as described earlier in this article. This process is dependent on the job site specification or expectations of the end user and should be tailored appropriately. A HEPA dust collector should be used to clean the concrete dust in between passes, as required by OSHA Silica regulations.
- Apply the required densifier or polishing guard product as required.
For the best results and to ensure safety and compliance with OSHA silica guidelines, Jon-Don recommends that concrete polishing only be done by trained concrete flooring professionals.
Jon-Don has a wide selection of concrete polishing equipment to help specialty concrete flooring professionals effortlessly polish concrete surfaces both large and small. We also have an extensive line of equipment available for rent on a daily, weekly, or monthly basis.
Concrete Polishing Training at Jon-Don
Looking to brush up on your concrete polishing skills? Our Concrete Polishing Training classes will teach you how to transform dull, boring concrete into a beautiful, polished work of art.
If you need one-on-one training on a new grinder or want to speak with one of our experts, we can’t wait to help. Give us a call at 800-556-6366.
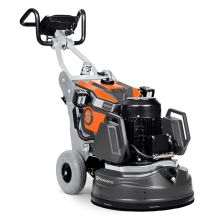
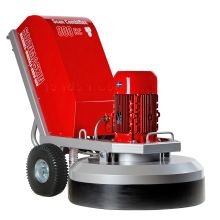
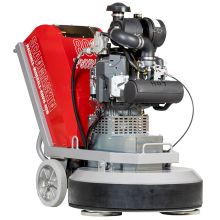
We pay the shipping charge, including hazardous material fees, on this item. There's no catch. No "buy this to get that" requirement.
Note: If your order contains items that are not eligible for free shipping, your order total will include our competitive shipping rates for those non-eligible items only. This shipping policy only applies to orders shipped within the Contiguous U.S.